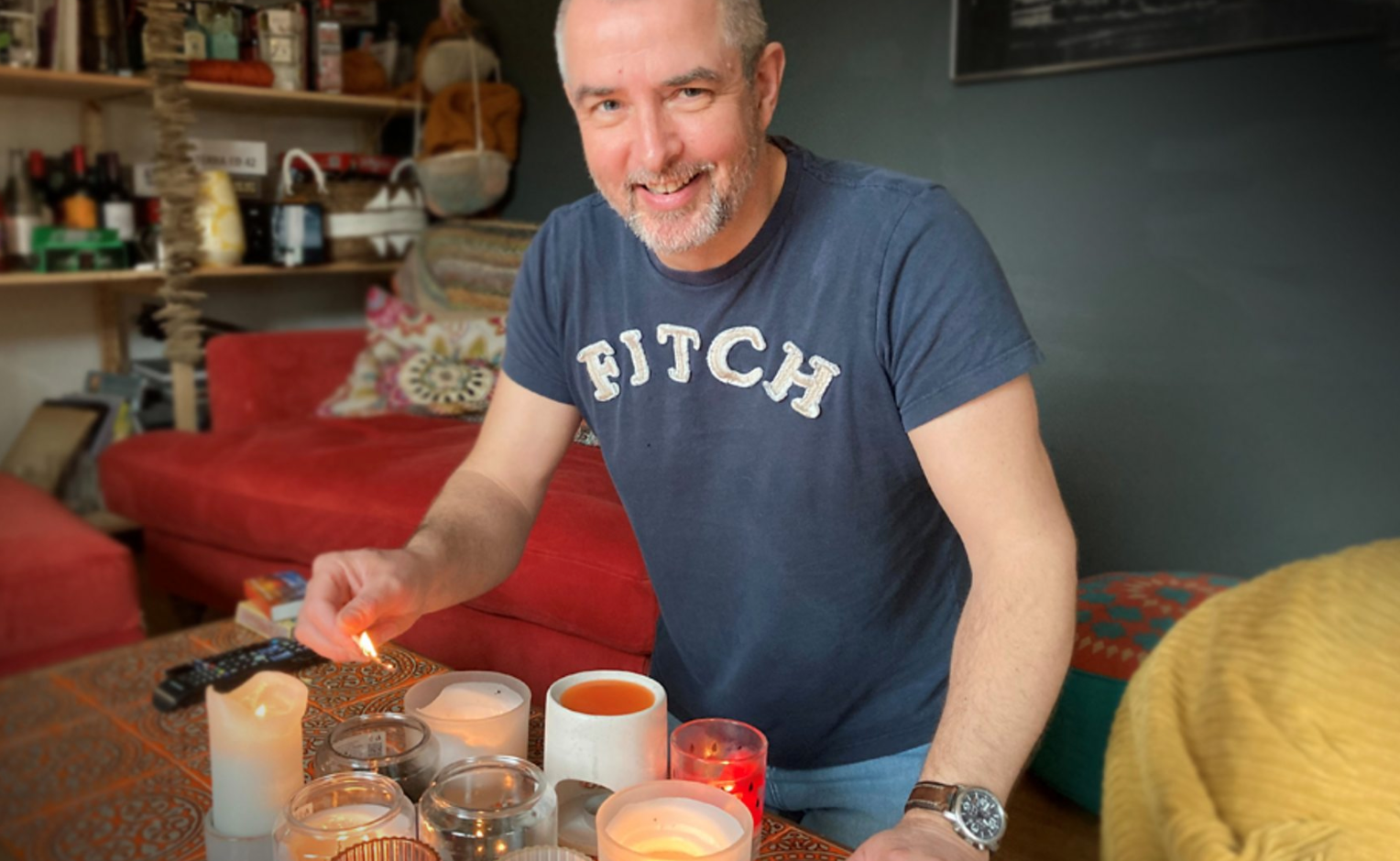
It was great to see this short piece from the BBC about a family heating their ‘Passivhaus’ home in Hickling with just a few candles! A group from Hudson Architects visited the site back in 2019 when the pair of semi-detached homes, designed by Anne Thorne Architects, were under construction.
The most interesting aspect of the project is the frame. This has been designed by Passivhaus Homes, (based in Totnes, Devon) using their PH15 system. It is a stick-built system, which uses the same composite joists in the wall and roof, and open-web posi-joists for the intermediate floor. The inner face of the wall and roof are lined with a medium-density vapour-permeable but airtight compressed wood-fibre panel, which also forms the web of the wall/roof joists. The outer face of the joists is finished with tongue-and-groove-jointed panels of low-density wood-fibre insulation. And the resulting 300mm void is then fully filled with blown cellulose insulation. The airtight fibre-board panels with their taped joints are continuous all the way up the inside of both storeys of the external wall, and across the underside of the vaulted roof, to form the continuous air-tight layer which is so crucial to passivhaus design. The floor joists are carried on a bearing-plate fixed to the inside face of the external wall in a ‘balloon-frame’ arrangement which greatly simplifies the airtight construction. This configuration avoids having to dress an air-barrier round the end of a floor zone built into the external wall, which is a weak-point in more common ‘platform-frame’ design.
Passivhaus Homes take the scheme drawings once planning permission is secured and do detailed design of the frame, producing a parts-list scheduled out from the from Revit model. This is sent to the Steico factory in Poland where a complete kit of pre-cut parts is manufactured – wall/roof and floor joists, inner and outer wood-fibre panels, and the triple-glazed windows – then shipped to the UK in a container for assembly on site. The Hickling project was built by Norwich-based Saint Columb Construction, who have built several other Passivhaus projects in Norfolk, including the Shangri La House at Waxham. They really liked the ‘kit of parts’ approach of the PH15 system, which we think could be a really good option for a hands-on self-build project.
Pic 1: A frame-model for another project using the same PH15 system by Passivhaus Homes.
Pic 2: The two houses under construction viewed from the garden of the adjacent straw bale house. You can see the deep composite joists and the dark green air-tight fibre-board on the inside face. On the ground floor, partly obscured by the hedge, you can see the straw-coloured panels of low-density wood-fibre insulation that will eventually seal in the first floor as well. The deep void between the wall and roof joists will be filled with blown cellulose insulation.
Pic 3: On the ground floor you can see the posi-joists overhead, and the green fibre-board airtight layer on the external wall. The vertical battens fixed to the fibre-board form a 25mm service void inside the airtight layer used for wiring. The open studwork on the left is the two acoustically separate layers of the party wall between the two semi-detached houses.
Pic 4: On the first floor you can clearly see the 300mm depth of the external wall and the airtight fibre-board with its taped-up joints. Over the window in the right-hand wall you can see the top of a plywood box-lintel, which arrives in pre-cut pieces and is assembled and filled with insulation on site. The roof joists meet the wall joists at a bisecting angle and are connected by a pre-cut angled ply-wood plate glued and screwed in place both sides of the join. There is no wall-plate at the eaves, so the insulated void is continuous up and over the roof.
Pic 5: The main wall voids are filled with blown cellulose insulation. Sheep-wool is used to fill smaller voids where the blown insulation can’t be used – in the lintels and in the narrow void around the window reveals.